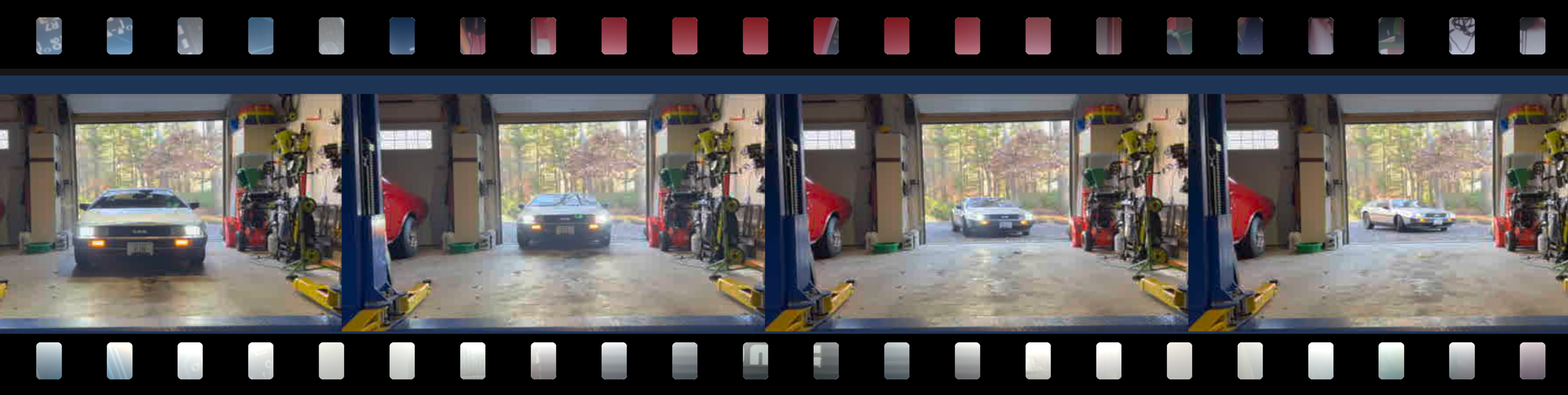
Videos
See how I’ve fixed and upgraded the DeLorean, and how I’ve built my other projects.
I’m working to add videos to older posts as well as creating new videos for new projects.
Now that the exhaust noise is fixed, I have to hunt down all the other noises I can hear now. One of them was the T-panel, which was resovled with a little bit of 3D printing.
Patrick and Bill Shea are the owners of the only privately-owned gold-plated DeLorean from DeLorean Motor Company itself. I went with North East Region DeLoreans to look at this car up close.
My steering wheel started rattling and sitting low. I went through all the usual suspects before trying to twist the cage, at which point it snapped in half in my hands. A quick bit of welding and it was all set.
A weird squeaking sound from my rear suspension led me to a failure on the right shock tower that needed to be fixed. The solution was my impact gun, some steel plate, a drill, and a 3D-printed die.
I need to be able to charge my phone in the DeLorean. I’m too lazy to plug in a cable and there’s no good place to rest it anyway, so I 3D printed a holder for the Apple MagSafe charging puck that replaces the ashtray.
I took my new suspension and exhaust for a test drive, but cut it short when a burning smell and a soft brake pedal told me that something was very wrong. A brake caliper had seized, but it wasn’t entirely clear just what had gone wrong.
My muffler had gotten rather loud, and then it started rattling. The former was a huge gash in the side of my muffler that I didn’t notice until I fixed the latter — the catalytic converter had broken apart. I wound up rebuilding most of the exhaust, and making it much quieter in the process.
I went into this with the goal of replacing the rear shocks with the KW coil-overs, but soon discovered that one of my trailing arms was basically made of rust. This led to a stainless steel trailing arm upgrade.
I had already refurbished the front suspension a couple years back, but I wanted to completely eliminate the vibrations I was seeing, so I went even further and replaced the entire thing with brand new, modern performance parts — billet alluminum LCAs, adjustable UCAs, KW shocks and resurfaced rotors.
My windshield washers stopped working, which wound up being a bad pump, bad harness, leaking bottle, and plugged washer nozzle. I fixed all of that and upgraded to dual nozzles mounted in front of the windshield, replacing the one on the wiper arm.
The DeLorean got louder than normal recently. This turned out to be a series of exhaust leaks involving broken welds, loose bolts, and worn flanges that all needed to be repaired or replaced.
The throttle position sensor on my 3.0L engine never worked properly, so I decided to address it with a custom 3D-printed mount for the valve cover. I tried PLA, PETG, and ASA filaments to see which would work best.
A new video, and a quick summary of the failures of the transmission linkage in my DeLorean.
I started noticing a coolant leak under the driver’s side of my car, to the left of the engine bay. It turns out that I had let a pipe rest on the frame and worn a hole in it, which had to be replaced. Bad routing from a former project also compromised the water pump hose, so that had to go to.
A quick swap of a bad O2 sensor wound up becoming a days-long process of waiting for tools, heating parts and finally removing the header and drilling out the bad unit. But it worked, and the new sensor is in reading good.
Angle drives break after five miles in my DeLorean, so I haven’t had a speedometer in years. Instead I built a clip-on digital one that picks up pulses from a Hall sensor passing by a VSS ring mounted on the rear axle, an Arduino, a 3D printed case and an Adafruit seven segment LED display backpack.
In order to get the rear of the DeLorean aligned, I had to swap out the perfectly good upper link arms with new adjustable ones. It was not as easy as it should have been, but became much easier after I got a new, more powerful impact gun.